【化工進展】生態環境部長江流域生態環境監督管理局生態環境監測與科學研究中心|李名揚,梁江北,謝衛民,等:廢鉛膏電沉積回收鉛技術研究進展與展望
廢鉛膏電沉積回收鉛技術研究進展與展望
李名揚1,梁江北2,梁莎2,謝衛民1,楊家寬2
1生態環境部長江流域生態環境監督管理局生態環境監測與科學研究中心,湖北 武漢 430010;2華中科技大學環境科學與工程學院,湖北 武漢 430074
引用本文
李名揚, 梁江北, 梁莎, 等. 廢鉛膏電沉積回收鉛技術研究進展與展望[J]. 化工進展, 2025, 44(2): 1042-1052.
?
DOI:10.16085/j.issn.1000-6613.2024-0123
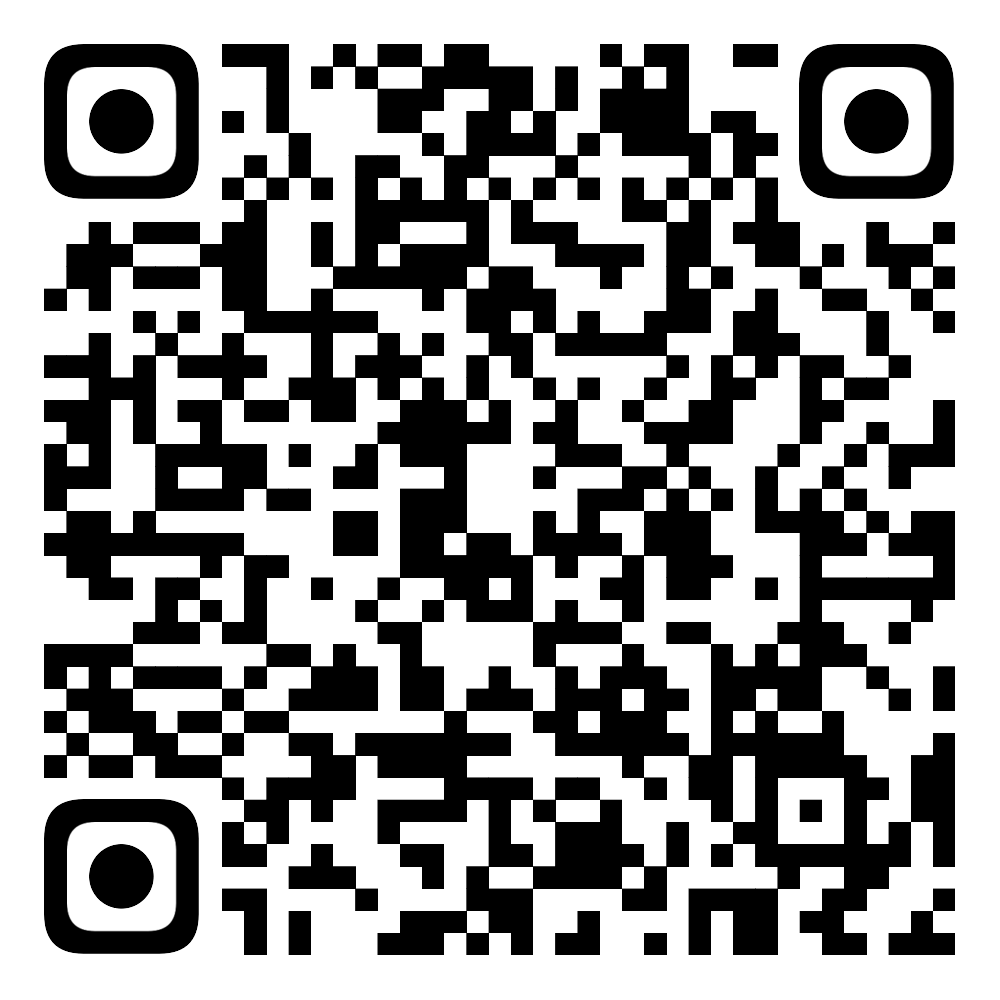
摘要
廢鉛酸蓄電池鉛膏是再生鉛的重要來源,傳統火法冶煉工藝產生鉛塵、二氧化硫及冶煉鉛渣,存在一定的環境風險,因此濕法工藝成為了研究的熱點。本文聚焦廢鉛膏濕法回收鉛工藝中的電沉積工藝,對酸浸出-電沉積、堿浸出-電沉積、其他溶劑浸出-電沉積、固相電解等工藝進行了綜述,對各工藝的原理、過程、技術參數進行了詳細分析。此外,本文對當前研究的電沉積回收鉛工藝的關鍵技術點,如廢鉛膏預處理方式、浸出/電解液體系、陽極副產物、電流效率及電解能耗、產物純度及形貌調控等進行了總結。同時,本文對電沉積工藝的前景進行了展望,認為浸出/電解液體系綠色環保、工藝流程短、電解能耗低、電解液可以循環利用,是廢鉛膏電沉積回收鉛工藝未來關注和研究的重點。
鉛是重要的金屬資源,對國民經濟發展起到了重要的支撐作用。近二十年來,全球精鉛產量一直呈現上升趨勢(圖1)。按照來源,鉛資源可分為原生鉛和再生鉛,原生鉛主要來源于礦山開采,如方鉛礦(PbS)、硫酸鉛礦(PbSO4)、白鉛礦(PbCO3)等;再生鉛主要來源于廢鉛酸蓄電池、鉛灰及含鉛冶煉渣等,其中廢鉛酸蓄電池占再生鉛來源的85%以上。隨著原生鉛礦資源的消耗,再生鉛成為鉛資源的重要來源。2022年,全球精鉛產量1481萬噸,其中再生鉛占65.4%,再生鉛占比持續升高;國內精鉛產量為614萬噸,再生鉛占比48.6%。國內再生鉛占比在近十年內持續快速提升,但相對全球平均水平仍有一定差距。
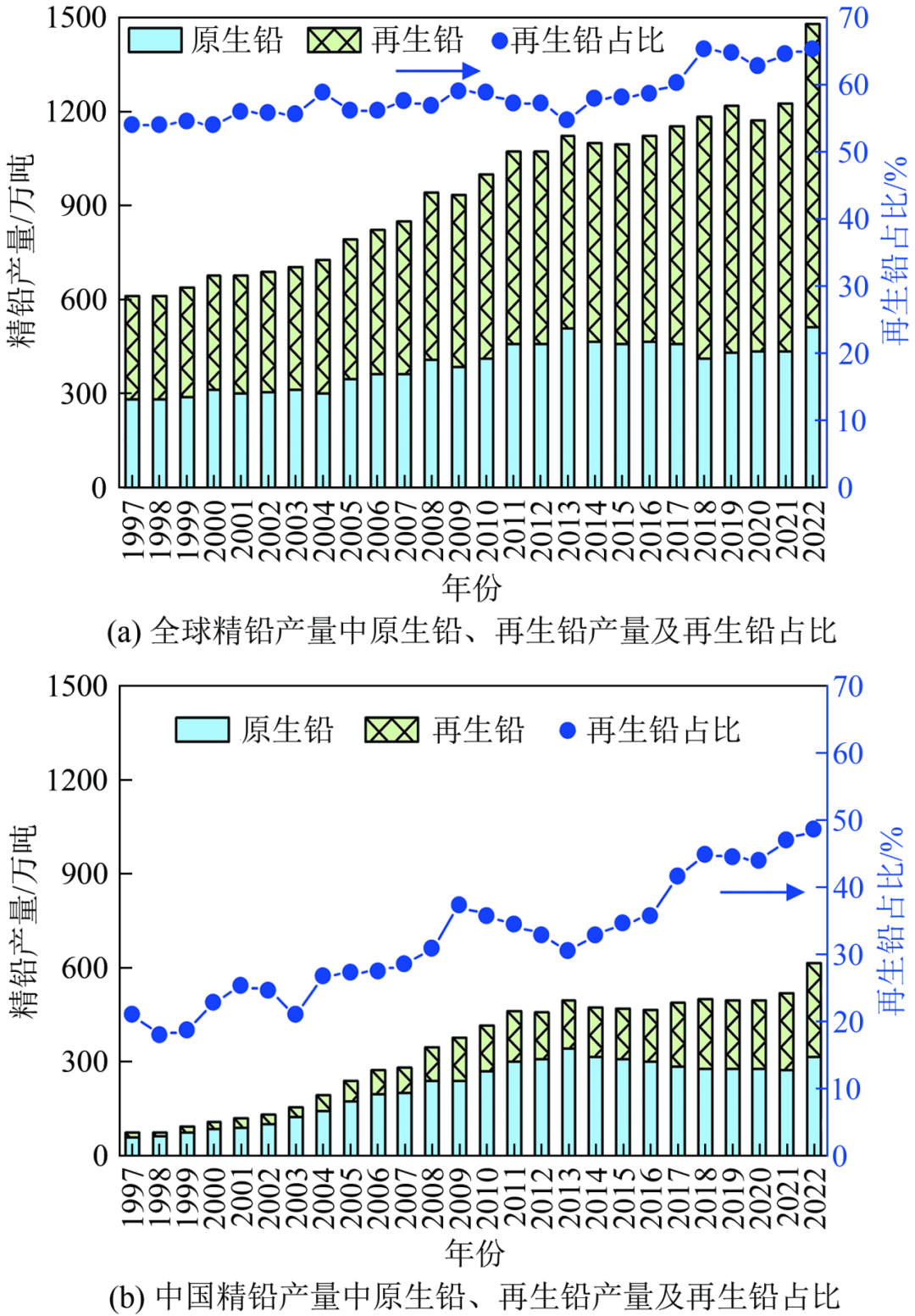
精鉛產量中原生鉛、再生鉛產量及再生鉛占比
廢鉛酸蓄電池是再生鉛的主要來源。廢鉛酸蓄電池中鉛含量高,含鉛組分可通過回收工藝進行再生。但是,鉛是有毒重金屬,廢鉛酸蓄電池已列入《國家危險廢物名錄》,如果回收過程處理不當,會對環境造成嚴重污染,對人體健康造成嚴重危害。因此,廢鉛酸蓄電池具有資源性和污染性雙重特性。
廢鉛酸蓄電池經過拆解、破碎預處理之后,主要分為廢鉛膏(30%~40%,質量分數,余同)、廢合金板柵(24%~30%)、廢塑料(22%~30%)以及廢硫酸(11%~30%)4個部分。其中廢鉛膏的主要成分包括硫酸鉛(約50%)、二氧化鉛(約28%)、氧化鉛(約9%)、金屬鉛(約4%)及微量雜質元素(Fe、Ba、Sb、Ca、Cu、Zn和Al等)。由于廢鉛膏中存在多價態的含鉛化合物,且硫酸鉛性質較為穩定,因此其成為廢鉛酸蓄電池處理中最難回收的部分。
針對廢鉛酸蓄電池拆解、破碎預處理后分離得到的廢鉛膏,主流回收工藝是火法冶煉,典型流程是廢鉛酸蓄電池分離出的廢鉛膏通過預脫硫得到硫含量低于1%的脫硫鉛膏,然后在1000~1200℃的溫度下進行熔煉,得到粗鉛錠,粗鉛錠經過300~700℃的精煉之后,得到精鉛產品。但火法冶煉過程產生了大量鉛塵、二氧化硫及冶煉鉛渣,存在較大的環境風險。
由于廢鉛膏火法再生冶煉工藝存在環境風險,更加綠色環保的濕法工藝成為了研究熱點。相較于火法工藝,濕法工藝避免了鉛塵和二氧化硫的產生。當前研究較多的濕法回收工藝主要包括化學轉化制備氧化鉛工藝、有機酸浸出-焙燒制備鉛粉工藝、電沉積回收金屬鉛工藝。化學轉化法主要是通過化學反應過程將含鉛組分向固相或者液相(浸出液)轉化,再通過焙燒或者結晶工藝轉化制備氧化鉛。有機酸浸出-焙燒制備鉛粉工藝是利用浸出過程中有機酸鉛結晶的原理,得到有機酸鉛結晶體,然后焙燒制備鉛粉。化學轉化法及有機酸浸出-焙燒制備鉛粉工藝各有優缺點,當前均處于實驗室研究或小試階段,距離實際應用還有一定距離。本文主要聚焦于電沉積工藝,電沉積工藝回收鉛研究起步早,經過不斷研究與發展,呈現了新的特點,具有較好的應用前景。本文重點對電沉積工藝的研究進展進行綜述,分析各種工藝的技術特點和待解決的問題,總結分析未來電沉積工藝需要突破的技術瓶頸,為電沉積工藝回收鉛技術研究提供參考。
01
電沉積工藝研究及應用進展
本文根據電沉積采用的浸出體系以及電沉積方式將目前的工藝分為4個類型,分別為酸浸出-電沉積工藝、堿浸出-電沉積工藝、其他溶劑浸出-電沉積工藝、固相電解工藝,工藝匯總及主要技術特征見表1,具體工藝特點見下文。
表1 廢鉛膏電沉積工藝匯總
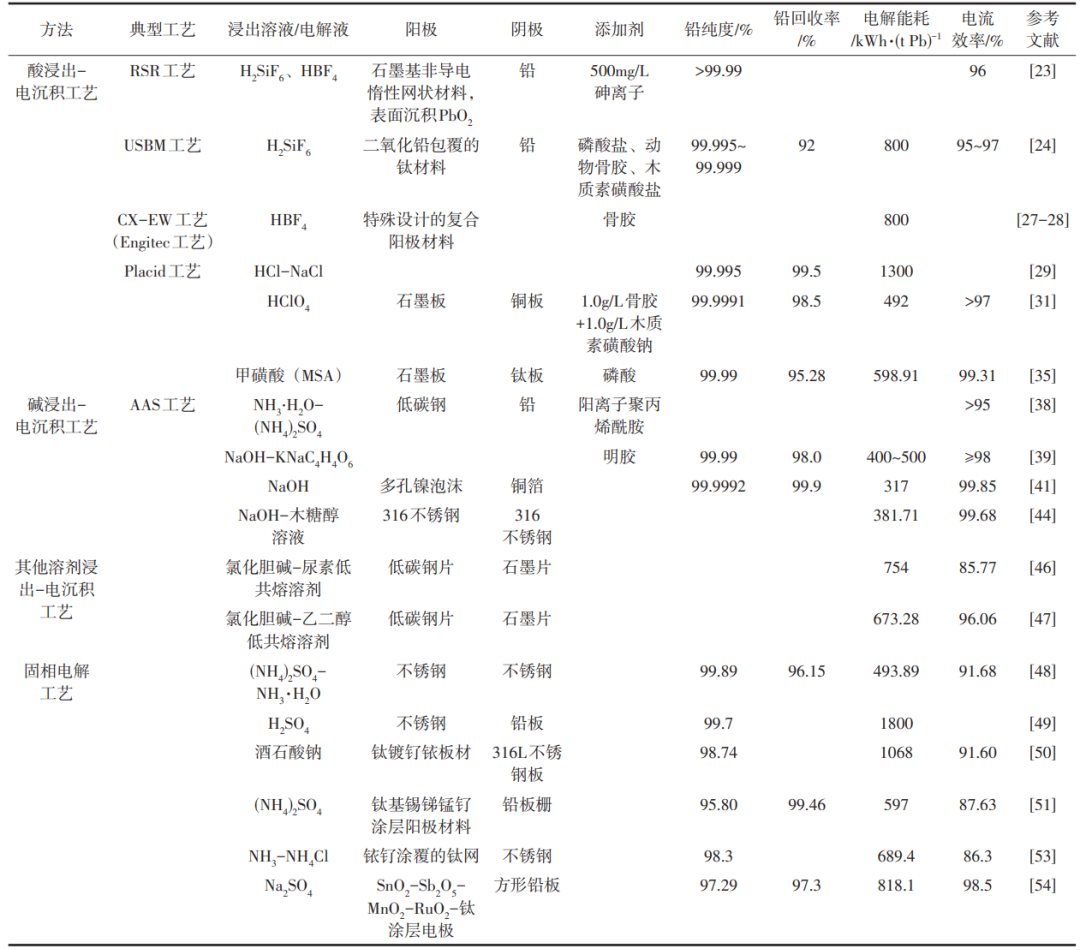
1.1 酸浸出-電沉積工藝
浸出-電沉積聯合回收金屬鉛是目前研究最多的工藝,技術研究最早開始于20世紀80年代,工藝主要是通過酸或堿浸出鉛膏,得到含鉛溶液,再通過電沉積,在陰極沉積金屬鉛。常見的酸性浸出劑有H2SiF6、HBF4、HCl-NaCl、HClO4、CH4O3S等。
氟硼酸和氟硅酸常用于廢鉛膏的浸出。David等提出了RSR工藝。該工藝主要包括脫硫、浸出、電沉積3個步驟(圖2),在脫硫工序中,碳酸鹽作為脫硫劑,而PbO2還原可以通過兩種方法,一種是通過亞硫酸鹽或者亞硫酸氫鹽作為還原劑,反應過程見式(1)、式(2);另一種方式是廢鉛膏經過290℃熱處理,PbO2分解為PbO。得到的脫硫鉛膏用氟硅酸和氟硼酸浸出,浸出液鉛離子濃度為70~200g/L。在電解過程中,添加砷離子能夠降低析氧電位,從而抑制陽極二氧化鉛的生成。在電沉積裝置中,陽極材料是石墨基底上覆蓋一層緊密貼合的非導電惰性網狀材料,隨后在材料表面沉積一層PbO2,使得陽極具有高導電性和穩定性,并且在HBF4或H2SiF6溶液中不易被侵蝕。在電流密度為216A/m2、槽壓為2.2V、電沉積時間為4h時,電流效率為96%,陰極得到99.99%高純度金屬鉛。浸出反應見式(3)~式(6),電沉積反應見式(7)、式(8)。
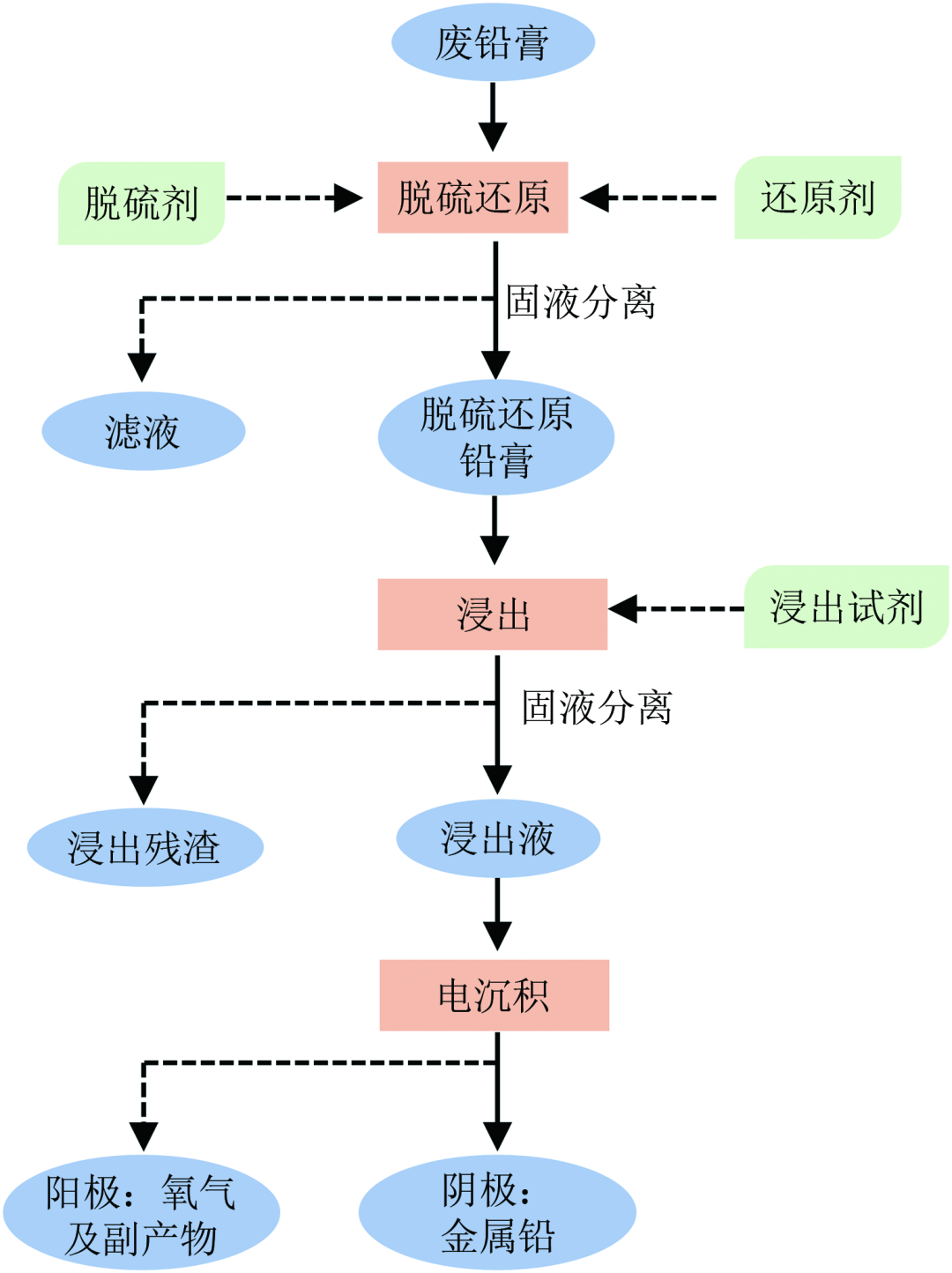
廢鉛膏脫硫還原-浸出-電沉積典型工藝流程圖
脫硫還原
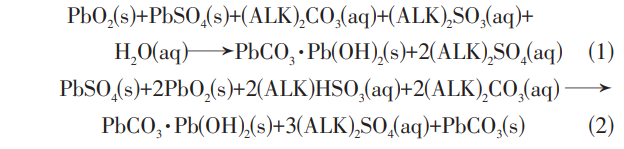
ALK代表堿金屬元素,是Alkali的簡稱。
浸出
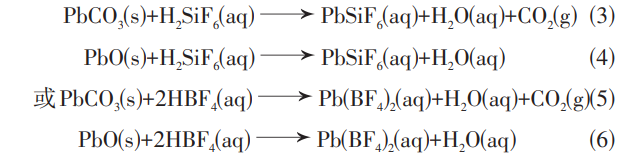
電沉積

Cole等提出了USBM電沉積工藝,其工藝過程與RSR工藝類似。不同的是,在氟硅酸浸出過程中,金屬鉛粉作為還原劑,使得二氧化鉛轉化成氧化鉛更易實現。電沉積過程中,二氧化鉛包覆的鈦材料作為陽極,鉛作為陰極。添加磷酸鹽用于抑制陽極二氧化鉛的生成,此外還添加0.05g/L動物骨膠和4g/L木質素磺酸鹽作為平整劑和晶粒細化劑。當電流密度控制在150~250A/m2時,電流效率達到95%~97%,電解能耗為800kWh/t Pb。但是RSR和USBM工藝均不能完全抑制陽極二氧化鉛的生成,相對較高的能耗以及酸的腐蝕依然是熱點問題。并且,氟硅酸在高于60℃的溫度下容易分解產生HF和SiF4,對操作人員及環境會造成危害。
Olper等也提出了用氟硅酸或氟硼酸作為浸出劑的CX-EW工藝,碳酸鈉或碳酸氫鈉作為脫硫劑,金屬鉛或雙氧水作為還原劑,隨后的電沉積過程類似。不同點在于,CX-EW工藝使用了一種特殊的復合陽極材料,該材料能在高電流密度下抑制陽極上PbO2的生成,同時溶液中殘留的H2O2有助于減少PbO2的生成,在320A/m2的電流密度下,電解能耗為800kWh/t Pb,在考慮回收浸出液中硫酸鈉的情況下,成本為210USD/t Pb。
除H2SiF6、HBF4浸出體系以外,HCl-NaCl也是一種重要的酸性浸出體系,被稱為Placid工藝,廢鉛膏通過HCl-NaCl溶液浸出,然后利用石灰中和浸出液中過量的酸制備石膏,過濾得到PbCl2溶液,通過加入單質鉛粉將其中的金屬雜質元素進行還原,過濾后的濾液進行電解,在陰極沉積得到金屬鉛。廢鉛膏主要成分與HCl-NaCl溶液反應過程見式(9)~式(11)。在Placid工藝中,電沉積得到的金屬鉛平均純度達到99.995%,鉛的回收率高達99.5%。但該工藝能耗較高,電沉積能耗達到1300kWh/t Pb,同時含氯浸出液對設備的腐蝕問題也不容忽視。

HClO4也被用于廢鉛膏浸出-電沉積回收鉛工藝。脫硫鉛膏與金屬鉛溶解于HClO4溶液,形成了HClO4-Pb(ClO4)2電解液,電沉積過程中,陰極得到金屬鉛,同時HClO4溶液可用于下一次浸出。該工藝電沉積能耗為492kWh/t Pb,能耗有所降低,金屬鉛的純度可達99.9991%,整個工藝鉛回收率大于97%。但HClO4也是一種強酸,腐蝕性問題依然存在。
甲磺酸(MSA)也常用于電解回收鉛。Wu等研究了甲磺酸回收白鉛礦中的鉛,首先使用甲磺酸浸出白鉛礦,初步浸出后,剩余的含鉛組分使用碳酸鈉脫硫,隨后再次經甲磺酸浸出,整個流程鉛的浸出率可以達到98%。在優化的電解參數條件下,陰極電流效率和電解能耗分別為99%和530kWh/t Pb。Chang等研究了甲磺酸浸出廢鉛膏回收鉛工藝,首先廢鉛膏中的硫酸鉛和二氧化鉛在碳酸鈉和亞硫酸鈉的作用下轉化成了Pb3(CO3)2(OH)2或NaPb2(CO3)2OH、PbO,脫硫后的鉛膏在MSA溶液中浸出,得到含鉛浸出液,最后電沉積得到金屬鉛并再生出MSA。在優化的條件下,可以獲得純度大于99.99%的扁平鉛板,并且鉛的總回收率達到95.28%,電流效率和電解能耗分別為99.31%和598.91kWh/t Pb,電解后的溶液可以作為浸出劑循環使用。與傳統的H2SiF6、HBF4、HCl-NaCl體系相比,甲磺酸體系具有高溶解度、低揮發性的特點,相對來說環境友好。熊睿等開展了甲磺酸浸出體系下基于隔膜電解槽的電沉積回收鉛研究,為了抑制陽極二氧化鉛的生成,使用陰離子交換膜將陰陽極室分隔,使得鉛離子不能遷移至陽極室發生氧化反應。在甲基磺酸鉛濃度0.4mol/L、電流密度200A/m2、乙酸丁酯添加量2.0g/L的參數條件下,電沉積得到平整致密的金屬鉛,電流效率為90.51%,電解能耗升高,為1011.78kWh/t Pb。
1.2 堿浸出-電沉積工藝
堿浸出-電沉積工藝中常用的浸出劑包括NaOH、NaOH-KNaC4H4O6、NH3?H2O-(NH4)2SO4等。
Etsell等提出了一種利用氨水-硫酸銨(AAS)浸出廢鉛膏的工藝(AAS工藝),在浸出過程中,PbO和PbSO4溶解于AAS溶液,而PbO2不溶于AAS溶液,可通過固液分離,然后利用熱的稀硫酸溶液(>80℃、>50%)將其轉化成PbSO4,隨后PbSO4可以再次返回到AAS溶液中。浸出液被輸送至一系列串聯的電解槽中,在陰極沉積得到海綿鉛,海綿鉛落到電解槽底部并被回收。完成電解后,電解液重新用于浸出步驟,同時富集的硫酸銨可以回收。該工藝使用氨水作為原料,因此需要完全密封避免NH3的揮發;回收產物是海綿鉛,而其他電沉積方法得到的是致密的金屬鉛;同時該工藝還原二氧化鉛的過程相對復雜。
NaOH-KNaC4H4O6可用于廢鉛膏的浸出。首先,廢鉛膏用NaOH脫硫,隨后在NaOH-KNaC4H4O6浸出體系下轉化成可溶含鉛溶液,見式(12)~式(13),未反應的PbO2與金屬鉛在Fe2+的作用下轉化成PbO,再返回至浸出體系。該體系鉛回收率達到98.0%,電沉積得到的鉛純度達到99.99%,電解能耗為400~500kWh/t Pb。
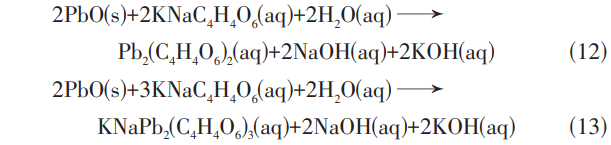
堿性浸出劑NaOH也用來溶解廢鉛膏,潘軍青等利用廢鉛膏中的二氧化鉛與單質鉛反應,在以SnSO4為催化劑的作用下,酸化反應獲得硫酸鉛,然后硫酸鉛溶解于20%~45%的NaOH溶液,見式(14)~式(15),通過電沉積,金屬鉛的純度可達99.9%,電解過程中陽極形成的PbO2磨細后可直接用作鉛酸蓄電池正極原料或添加劑。隨后研究人員對該工藝進行了改進,通過催化轉化和堿性脫硫直接獲取含鉛堿性電解液,利用陽離子交換膜避免電解過程中HPbO2-遷移至陽極室轉化成PbO2。通過對該工藝系統性研究,在優化的參數條件下,電解槽壓能降到1.23V,電流效率能達到99.85%,電解能耗為317kWh/t Pb,電沉積得到的金屬鉛純度達到99.9992%,鉛回收率達到99.9%。

為了減少還原劑鉛粉和脫硫劑NaOH的使用量,該工藝進行了進一步改進。廢鉛膏水洗去掉殘酸之后,直接與過量的NaOH溶液反應,得到Na2[Pb(OH)4]與NaOH混合溶液和Pb與PbO2混合固體。堿性含鉛溶液在離子交換膜電解槽中電沉積得到金屬鉛,Pb與PbO2混合物通過固相電解得到鉛粉。
該文作者課題組還利用堿性浸出液構建了一種H2-PbO燃料電池用于回收鉛(圖3)。首先,廢鉛膏溶解于熱的NaOH溶液形成可溶NaHPbO2溶液,隨后NaHPbO2溶液在陰極室通過電沉積得到金屬鉛,最后陽極H2氧化得到H2O,電化學反應見式(16)~式(18)。該方法得到的金屬鉛純度可達99.994%。但是該方法使用較為昂貴的納濾膜以及陽極氫氣催化氧化材料,難以推廣應用。
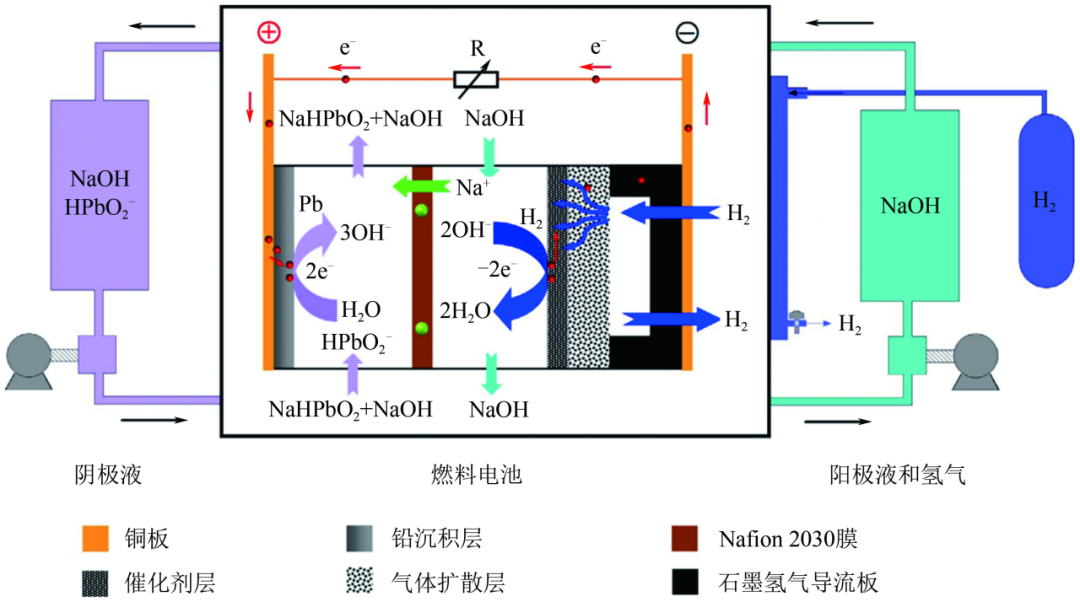
H2-PbO燃料電池原理圖
負極

正極

總反應

堿性木糖醇體系(NaOH-木糖醇溶液)被用于電沉積回收鉛。廢鉛膏中的PbO2可在木糖醇的作用下還原成PbO,PbSO4可溶解于NaOH溶液中,廢鉛膏在NaOH-木糖醇溶液中的溶解率可以達到96.24%。堿性木糖醇體系電沉積實驗結果表明,在電流密度140A/m2、溫度40℃、NaOH濃度100g/L、木糖醇濃度120g/L、溶液Pb2+濃度100g/L、極距4cm、流速15mL/min條件下,電流效率可達99.68%,陰極電解能耗可達381.71kWh/t Pb,生成的陰極鉛表面相對平整,枝晶較少。
1.3 其他溶劑浸出-電沉積工藝
低共熔溶劑(deep eutectic solvents,DESs)是由兩種或兩種以上組分通過氫鍵的作用相互締合而形成的低共熔混合物,其具有良好的熱穩定性和較寬的電化學窗口,被認為是新一代綠色溶劑。低共熔溶劑也被用于電解回收鉛,耿笑等研究了以氯化膽堿-尿素低共熔溶劑為電解液,電化學回收廢鉛膏制備鉛粉的新工藝。在槽電壓為2.5V時,陰極電沉積得到的金屬鉛形貌為棒狀,電流效率達到85.77%,電解能耗為754kWh/t Pb。
黃皓銘等研究了以氯化膽堿-乙二醇低共熔溶劑為電解質,從廢鉛膏中電沉積回收鉛的方法。低碳鋼片和石墨片分別作為陰極和陽極,在2.5V恒定電壓、電解液溫度90℃條件下,30g/L廢鉛膏溶解于溶劑體系中,電流效率為96.06%,電解能耗為673.28kWh/t Pb,電沉積陰極產物為金屬鉛,形貌主要為棒狀。
1.4 固相電解工藝
固相電解法是將廢鉛膏調配成膏狀物質涂在陰極板上,在不同的電解液體系下,陰極含鉛化合物直接轉化成金屬鉛。固相電解工藝的原理如圖4(a)所示。陰極反應是廢鉛膏中的不同含鉛化合物(硫酸鉛、二氧化鉛、氧化鉛)轉化成金屬鉛,陽極反應主要是電解水產生氧氣。與浸出-電沉積工藝相比[圖4(b)],固相電解工藝主要區別體現在陰極上,浸出-電沉積工藝過程中,電解液中的鉛離子在溶液中遷移,在電極材料表面發生電沉積反應。
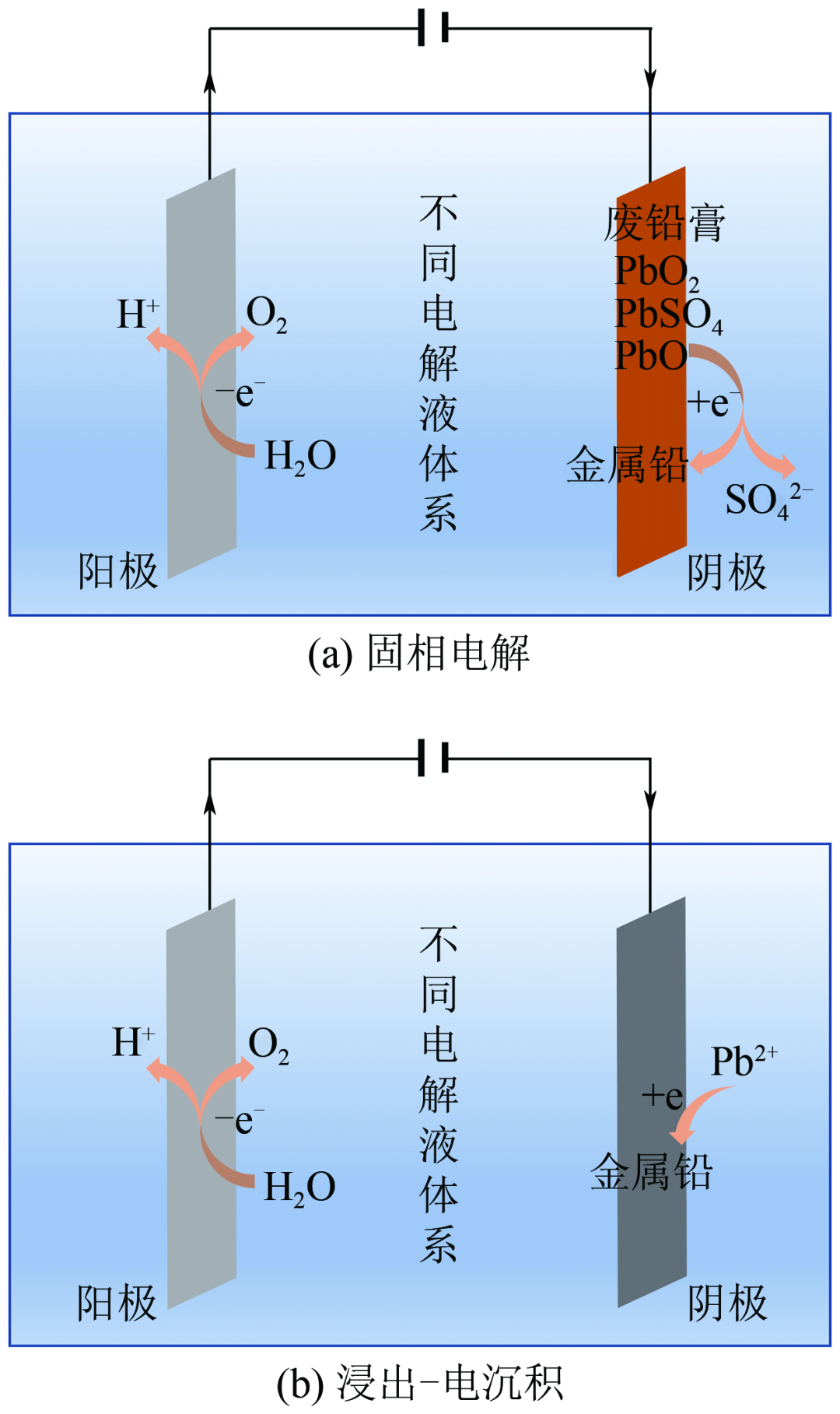
固相電解及浸出-電沉積工藝原理圖
(NH4)2SO4-NH3·H2O緩沖溶液可用于固相電解回收鉛。廢鉛膏加水濕潤后平鋪在不銹鋼陰極上,(NH4)2SO4-NH3·H2O緩沖溶液作為電解液,廢鉛膏中的含鉛化合物(PbSO4、PbO2、PbO)在陰極得電子析出海綿狀鉛,見式(19)~式(22)。陽極反應見式(23)。海綿狀鉛通過熔融精煉得到精鉛。在優化的電解參數條件下,電流效率達到91.68%,電解能耗為493.89kWh/t Pb。制備的金屬鉛純度達到99.89%,工藝鉛回收率為96.15%。
陰極


陽極

胡彪等研究了廢鉛膏直接電解回收金屬鉛工藝,電解過程中,陰極為鉛板,廢鉛膏平鋪壓實置于鉛板上,陽極為不銹鋼板,電解液為硫酸溶液。在電解過程中,陰陽極主要電化學反應見式(24)~式(29)。該工藝在優化的參數條件下,如硫酸密度為1.20g/cm3、電流密度為637A/m2時,電解能耗可以控制在1800kWh/t Pb,獲得的電解鉛純度可達99.7%。
陰極
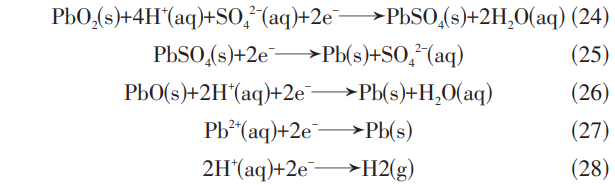
陽極

酒石酸鈉被證明可以用于固相電解回收鉛。在酒石酸鈉濃度為1.0mol/L、電流密度為375A/m2等條件下,電流效率為91.60%,電解能耗為1068kWh/t Pb,陰極鉛純度達到98.74%,電解液可以通過補充一定量氫氧化鈉來循環利用。
硫酸銨體系也被用于固相電解。漿化后的廢鉛膏均勻涂覆在網格狀的鉛板柵上,然后將板柵進行真空干燥固化,電解過程中,涂抹廢鉛膏的鉛合金板柵為陰極,鈦基錫銻錳釕材料為陽極,該固相電解過程中,PbSO4還原為Pb的電化學過程為PbSO4先溶解為Pb2+,Pb2+還原成Pb晶粒,整個過程屬于電化學-擴散混合控制下的三維形核,擴散作用發揮主要貢獻。在200g/L (NH4)2SO4溶液、電流密度為200A/m2的優化條件下,電解產物中鉛含量達到95.80%,電流效率87.63%,電解能耗為597kWh/t Pb,金屬鉛的回收率達到99.46%。
Fan等采用NH3-NH4Cl體系直接固相電解回收鉛,模擬廢鉛膏壓制成圓片狀,然后固定在不銹鋼陰極上,使用銥釕涂覆的鈦網作為陽極,用氨水將NH4Cl溶液的pH調節為7.5,在NH3·H2O-NH4Cl電解液體系中,2.30V的恒定電壓條件下電解3h,圓片中的鉛含量達到98.3%,電流效率為86.3%,電解能耗為689.4kWh/t Pb。
Wang等提出一種使用袋裝陰極固相電解回收鉛工藝,以硫酸鈉溶液為電解液,廢鉛膏中的硫酸鉛可通過溶解-電沉積和直接固相電沉積的方式還原成金屬鉛,二氧化鉛還原成中間產物如3BS(3PbO·PbSO4)或者氧化鉛,然后還原成金屬鉛。在電流密度為200A/m2、電解液溫度為60℃條件下,陰極電流效率為98.5%,脫硫率99.6%,鉛回收率97.3%,電解能耗為818.1kWh/t Pb,電沉積鉛產物的純度為97.29%。
02
電沉積回收鉛技術特點
2.1 廢鉛膏預處理方式
由于廢鉛膏中含鉛組分主要包括硫酸鉛、二氧化鉛、氧化鉛、金屬鉛,鉛元素價態不一,同時硫酸鉛和金屬鉛難溶于酸,因此在溶劑浸出-電沉積工藝中,為了便于浸出,需要對廢鉛膏進行預處理。預處理包括硫酸鉛的脫硫轉化、二氧化鉛的還原、金屬鉛的氧化。由于金屬鉛含量占廢鉛膏比重較小,而且容易在后續反應步驟中逐漸被氧化,因此金屬鉛的氧化不需要重點考慮。硫酸鉛的脫硫是預處理過程中需要重點考慮的步驟,一般思路是利用碳酸鹽將硫酸鉛轉化成碳酸鉛,從而方便后續酸浸出。在堿浸出工藝中,硫酸鉛可直接在過量的堿液中轉化成可溶的鉛酸氫鹽。針對二氧化鉛的還原,常采用雙氧水、金屬鉛粉、亞硫酸鹽或亞硫酸氫鹽等還原劑,也可以考慮通過加熱分解的方式將二氧化鉛轉化成氧化鉛。
脫硫還原步驟的先后或者同步進行,關乎預處理流程的復雜程度。先脫硫后還原步驟中,一種是考慮逐步實現含鉛物質的轉化,另一種是考慮在脫硫及浸出步驟中,二氧化鉛不發生轉化,后續工藝分離出來的二氧化鉛單獨處理,再返回至工藝流程中。脫硫與還原也可以同步實施,例如碳酸鹽和亞硫酸鹽、亞硫酸氫鹽體系,氯化鈉和鉛粉(還原劑)體系。
2.2 浸出/電解液體系
廢鉛膏電沉積回收鉛工藝中的浸出劑或電解液種類較多,如酸性浸出劑H2SiF6、HBF4、HCl-NaCl、HClO4、CH4O3S等,堿性浸出劑NaOH、NaOH-KNaC4H4O6、NH3?H2O-(NH4)2SO4、NaOH-木糖醇等,其他溶劑包括氯化膽堿-尿素、氯化膽堿-乙二醇等低共熔溶劑,固相電解過程中使用的電解液包括NH3?H2O-(NH4)2SO4、(NH4)2SO4、Na2SO4、NH3-NH4Cl、硫酸、酒石酸鈉等。不同浸出/電解液體系使得工藝呈現不同特點,包括酸堿性、腐蝕性及揮發性、對含鉛化合物的溶解性。
在上述浸出/電解液體系中,H2SiF6、HBF4、HCl-NaCl、HClO4都屬于強酸,具有強腐蝕性,氟硅酸在高于60℃的溫度下容易分解產生HF和SiF4,HCl、HBF4和HClO4溶液具有強腐蝕性、強刺激性,這些強酸性浸出體系會在實際規模化應用過程中對設備造成較強的腐蝕,增加工藝成本。同時,這些酸基本都具有一定的揮發性或者強刺激性,需要在相對密封的條件下進行,避免對操作人員的危害。使用較多的堿性浸出劑是NaOH,其對硫酸鉛和氧化鉛具有較好的溶解性,浸出效率較高,但值得注意的是,氫氧化鈉具有強堿性,腐蝕性極強,同時工藝過程中的NaOH溶液的碳酸鹽化也值得關注。堿性浸出體系中,以NH3?H2O-(NH4)2SO4為浸出劑時,需要考慮完全密封,避免NH3的揮發。
不同的浸出劑對含鉛化合物的溶解能力不同,從而影響鉛的浸出率以及電解液中鉛離子濃度。RSR工藝中鉛濃度控制在70~200g/L,USBM工藝中鉛濃度為25~150g/L,CX-EW工藝鉛濃度為50~100g/L,Placid工藝中鉛濃度為25g/L,HClO4浸出工藝中,優化條件下鉛濃度為82g/L,甲磺酸體系下,鉛濃度為50~150g/L。以上不同鉛濃度范圍主要是由浸出體系對鉛的溶解性以及電沉積優化的工藝參數共同決定的。
2.3 陽極產物二氧化鉛
在鉛電沉積過程中,陰陽極發生的主要電化學反應見式(30)~式(33),其中陽極通常會發生副反應生成PbO2,這對電沉積回收目標金屬鉛來說是不利的,研究人員通常采取不同方法避免陽極PbO2的生成,例如添加電解液添加劑、選用不同的陽極材料和設置電解槽隔膜。
通常使用的電解液添加劑包括砷離子、磷酸鹽、雙氧水、鈷鹽等,這些添加劑通過降低析氧電位使析氧反應優先發生,從而抑制陽極二氧化鉛的生成。通過選用不同的陽極材料也可以抑制二氧化鉛的生成,例如CX-EW工藝中,使用了一種特殊的復合陽極材料,該材料能在高電流密度下抑制陽極上PbO2的生成。通過在電解槽中設置陰離子交換膜,使得鉛離子不能遷移至陽極室發生氧化反應,也是避免陽極二氧化鉛生成的有效方法,但該方法增加了膜材料的成本,同時提高了電解槽的槽壓,使得電解能耗增加。
陰極

陽極

2.4 電流效率及電解能耗
電流效率及電解能耗是電沉積工藝的關鍵性參數。電沉積過程中,電流效率和電解能耗的計算方法見式(34)、式(35)。
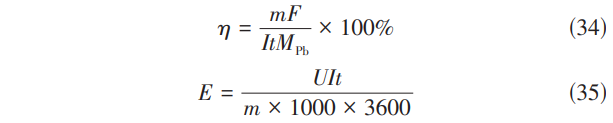
式中,η為電流效率,%;E為電解能耗,kWh/g;m為鉛產物的質量,g;U為電壓,V;I為電流,A;t為電解時間,s;F為法拉第常數,96485C/mol;MPb為鉛的原子量,207.2。
不同的電沉積體系電流效率和電解能耗有所不同,但普遍來說,電流效率在優化的工藝參數條件下能達到86%~99%的較高水平。從已有的文獻看,固相電解的電流效率略低,在86.3%~98.5%之間,酸浸出/堿浸出-電沉積工藝的電流效率較高,在95%~99.8%之間,而堿性體系的電流效率更高一點。
不同工藝的電解能耗相差較大,最低為317kWh/t Pb,最高能達到1800kWh/t Pb,在電流效率普遍較高的情況下,電解能耗與電解過程中的電壓相關,以電解能耗最低的317kWh/t Pb為例,其電解的槽壓僅為1.23V,而電解能耗最高的1800kWh/t Pb,其電解槽壓能達到4V以上。電解槽壓是由液相傳質和電化學轉化過程決定的,具體與電沉積過程中的電流密度、離子活度、電解液溫度、電極間距等因素相關。電流密度、電極間距增大,會導致電解槽壓上升;電解液溫度升高,在電流密度不變的情況下,槽壓呈現下降趨勢。因此,需要通過參數優化實驗來確定最佳的工藝參數。較高的電流效率和較低的電解能耗關系到電沉積工藝的成本,對工藝的實際應用潛能影響較大,其是評價電解工藝最關鍵的指標之一。
2.5 電沉積產物純度
電沉積陰極鉛的純度普遍較高,可以達到95%~99.999%,這主要是由兩方面原因決定的。一是雜質金屬元素含量低。廢鉛膏中鉛組分含量高,雜質金屬元素(如Fe、Ba、Sb、Ca、Cu、Zn和Al等)含量低,屬于微量元素,在浸出過程中鉛組分進入浸出液,同時微量雜質元素在浸出過程中部分進入浸出液。總體而言,鉛離子含量為g/L級別,而雜質元素含量為mg/L級別。二是金屬元素電沉積的電壓窗口不一致。廢鉛膏包含的幾種微量雜質元素,從標準電極電勢來看,在陰極沉積由難到易的順序為:Ba2+、Ca2+、Al3+、Zn2+、Fe2+、Pb2+、Fe3+。這為判斷不同金屬雜質元素在電沉積過程中的難易程度提供了理論指導,但由于浸出體系不同,金屬絡合離子不一樣,金屬電沉積的先后順序會有所不同。整體而言,鉛離子電沉積是相對較為容易的,這樣使得電沉積具有一定的選擇作用,電沉積鉛產物純度較高。
2.6 電沉積產物形貌調控
電沉積產物的形貌是關乎電沉積產物質量的一個關鍵指標,一般情況下是期望得到平整致密的金屬鉛。電解液添加劑在陰極電沉積產物形貌調控方面起著至關重要的作用。在不含添加劑的電解液中,陰極產物呈現樹枝狀或毛刺狀,這種現象會影響電沉積槽電壓,嚴重情況下會影響電沉積裝置的運行。目前報道的電解液添加劑主要包括:①膠質類,如骨膠;②有機陰離子類,如木質素磺酸鈉;③中性有機分子,如酯類、酚類、芳香烴等;④表面活性劑類,如烷基磺酸以及各種氨基酸。通過添加一種或多種電解液添加劑,使得電沉積產物形貌滿足要求。諸多研究表明,添加劑的作用被歸因于提高陰極鉛沉積的過電位,可以增加成核數量,起到細化晶粒的作用。除了采用添加劑來調控電沉積產物形貌以外,電沉積工藝參數(如電流密度、鉛濃度)也會對電沉積產物的形貌產生影響。在電沉積過程中,金屬鉛的微觀形貌會呈現顆粒狀、棱柱狀、樹枝狀等,這些微觀形貌的差別是由各類因素主導下的晶體晶面生長差異造成的。
03
電沉積工藝前景展望
通過綜述不同電沉積工藝以及分析工藝特點,可以說明不同的電沉積工藝各有優缺點,工藝越來越趨向于簡便化、經濟性和環境友好性。以下總結未來電沉積工藝需要考慮的幾個重點方面(圖5)。
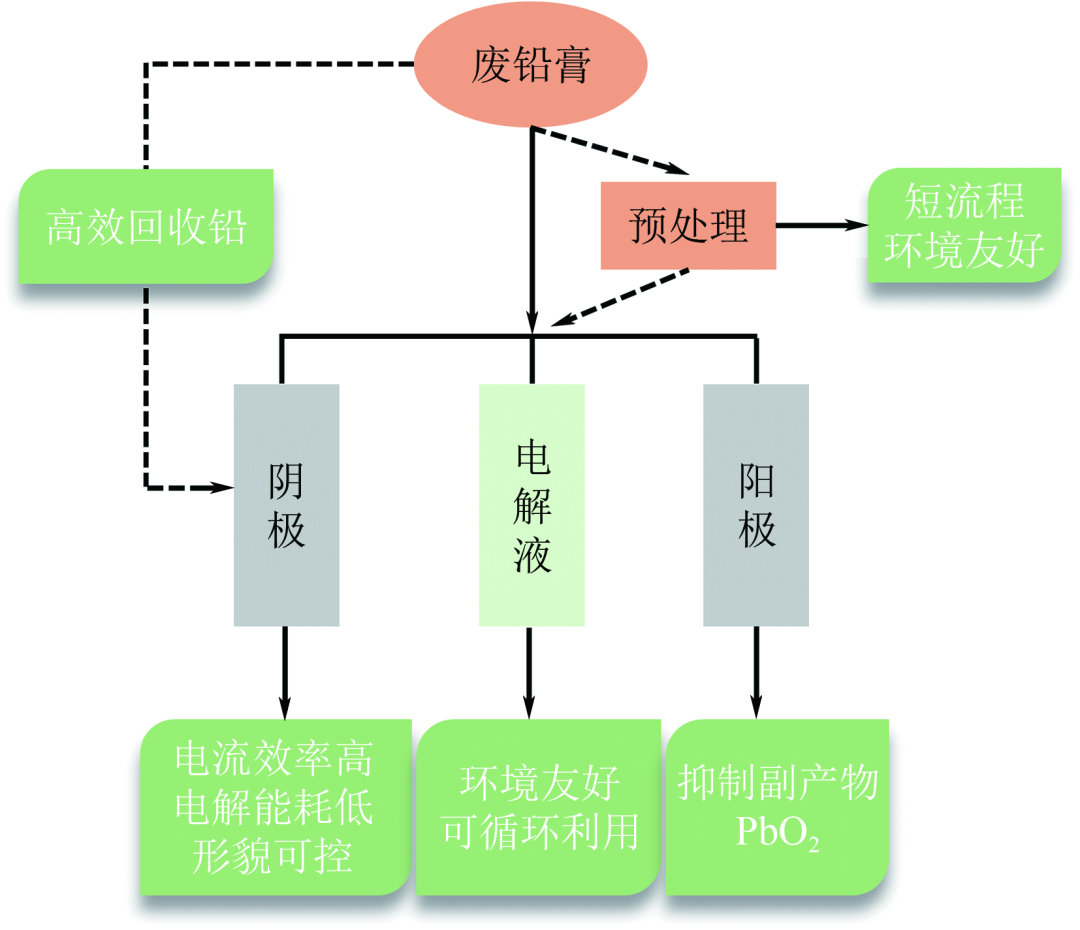
廢鉛膏電沉積回收鉛工藝展望
(1)浸出體系的環境友好性。目前,研究的電沉積工藝浸出劑大多數是強酸強堿,酸堿的腐蝕性關乎設備成本、人員操作環境和安全性。一些相對環境友好的酸或溶劑應重點關注和研究。
(2)工藝流程的復雜性和回收效率。電沉積工藝中,酸性電解液體系步驟相對復雜,包括脫硫、還原、浸出和電沉積等步驟;堿性體系可以實現脫硫與浸出同步進行,工藝相對簡單。在后續的研究中,若實現廢鉛膏短流程轉化,將大大降低工藝的復雜性,有利于提升鉛的轉化率及回收率。
(3)電解工藝的電流效率及能耗。電流效率及電解能耗關乎電沉積工藝實際應用潛力,目前電沉積工藝電解能耗為300~1800kWh/t Pb,這主要是由電解液體系以及電解方式決定的,例如堿浸出-電沉積工藝能耗相對較低,固相電解工藝能耗相對偏高。電沉積能耗的控制是工藝可以實際應用的重要前提。
(4)陽極二氧化鉛的抑制。在電沉積過程中,當陽極生成的二氧化鉛作為非目標產物時,二氧化鉛的控制是需要重點關注的。一般情況下,通過添加劑不能完全抑制二氧化鉛的生成,而設置離子交換膜會增加電解槽壓,增加電解能耗。通過選用合適的陽極材料或者材料改性,可以減少二氧化鉛的生成,但也會增加電極材料的成本。因此,陽極二氧化鉛的抑制可能需要采取綜合的手段進行調控。
(5)電沉積產物形貌的調控。電沉積過程中,可能會生成海綿狀鉛,使得鉛在陰極的附著力較差,需要從陰極泥中回收金屬鉛。而普遍情況是,鉛沉積過程中形成較為嚴重的枝晶,其會影響電沉積的槽電壓,嚴重情況下會影響電沉積裝置的運行。因此,形成平整致密的金屬鉛是電沉積回收金屬鉛的主要思路。
(6)電解液循環利用。目前已有研究對電解液的循環利用關注較少,僅僅從工藝的流程角度,對電解液循環利用的可行性進行了初步判斷,而對循環利用效果、電解液試劑的損耗程度、雜質金屬元素的富集等沒有開展具體研究,因此為了有效降低浸出試劑的損耗,需要重點研究電解液循環利用問題。
04
結語
本文對酸浸出-電沉積、堿浸出-電沉積、其他溶劑浸出-電沉積、固相電解等廢鉛膏電沉積回收鉛工藝進行了綜述,對各工藝的原理、過程、技術參數進行了總結,分析了各工藝的優缺點。此外,對電沉積回收鉛工藝中廢鉛膏預處理方式、電解液體系選擇、陽極副產物、電流效率及電解能耗、產物純度及形貌調控等關鍵技術點進行了剖析,并對電沉積工藝的前景進行了展望,指出了實現浸出溶劑(電解液體系)綠色環保、工藝流程短、電解能耗低、電解液可循環利用的廢鉛膏電沉積高效回收鉛工藝是未來關注和研究的重點。
作者簡介
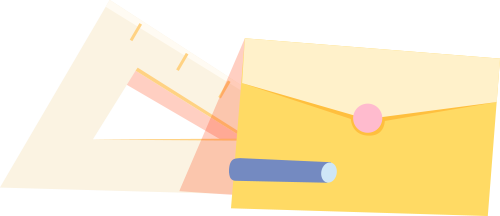
第一作者:李名揚,博士,高級工程師,研究方向為固廢資源化。
通信作者:謝衛民,高級工程師,研究方向為固廢資源化。